Classification of sandwich panels by core material
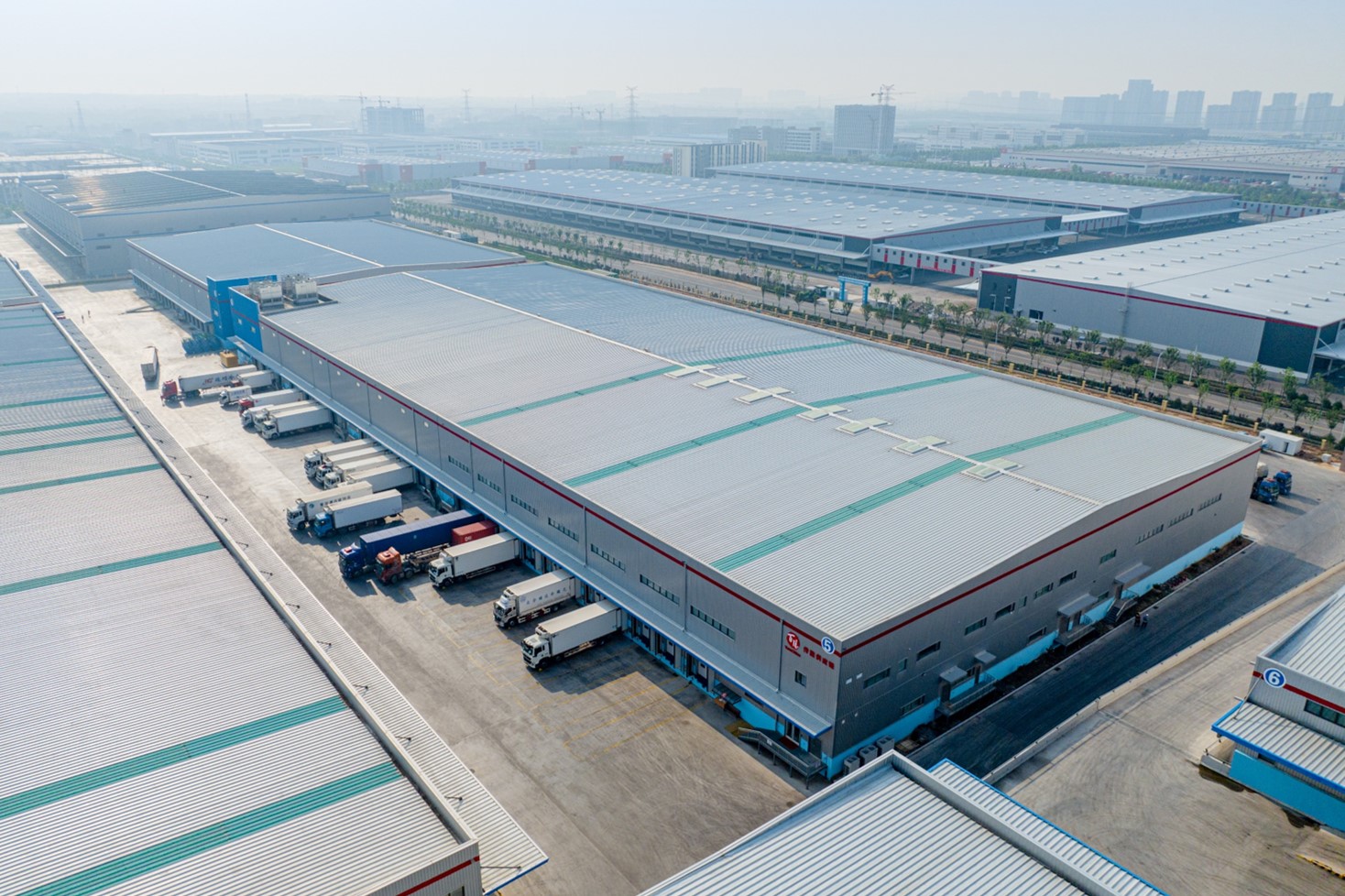
Sandwich panels are composite materials used in a diverse range of construction and engineering applications. The panels are formed using two sheets of strong, thin metal (steel, stainless steel or aluminum) bonded between a core material. There are several types of core materials, including polyisocyanurate (PIR), polyurethane (PU), expanded polystyrene (EPS), rockwool, and composite honeycomb. The core material, in combination with material strength and corrosion resistance of the metal sheets, determines the suitability of different sandwich panels for various construction applications.
Polyisocyanurate (PIR)
Polyisocyanurate (PIR) is a cured form of polyurethane, and is the most commonly used material in the production of sandwich panels. PIR is a lightweight, rigid foam that has high insulation properties and excellent fire resistance. It is also moisture-resistant and relatively low-cost due to its widespread use in the manufacture of building insulation products. PIR core panels are well-suited for uses such as roofing systems, wall insulation, and floor insulation due to their low thermal conductivity and structural stability.
Polyurethane (PU)
Polyurethane (PU) core panels are similar to PIR in many ways, and offer similar characteristics such as high insulation values and excellent resistance to fire. However, PUR panels are usually not as lightweight as PIR, and therefore have slightly lower insulation properties and higher costs. As such, they are more often used in situations where the additional strength and durability of PUR is necessary, such as in hi-load roofing. PU panels are also optimal for areas where a higher initial thermal resistance (R-value) is required, as the foam is better at retaining heat.
Expanded Polystyrene (EPS)
Expanded polystyrene (EPS) is commonly used in the manufacture of insulation products, such as wall and floor insulation panels. This is because it offers excellent thermal resistance similar to PIR and PUR, but is even lighter and more cost-effective. EPS also has a high compressive strength, making it suitable for use in high-load applications such as walls and floors. Additionally, the foam does not contain medically hazardous substances, making it a popular choice for indoor applications. However, EPS is not as resistant to moisture or fire as PIR or PUR, making it less suitable for certain construction applications.
Rockwool
Rockwool is an inorganic material made from molten rocks and slag. Compared to other core materials, it is more rigid and has significantly higher thermal resistance due to its mineral composition. As a result, rockwool panels are often used in applications requiring excellent insulation, such as roofing and wall insulation. They are also approved for use as fire barriers in high-risk areas due to their superior fire resistance. However, because of their weight and brittleness, rockwool panels are not suitable for applications that require significant structural stability.
Composite Honeycomb
Composite honeycomb is a lightweight material made from more than one layer of polymer sheets and a honeycomb core. Due to its high strength and low weight, composite honeycomb is used in the construction of high-load structures such as aircraft and automobiles. The material is also very rigid and has excellent acoustic and thermal insulation properties, making it suitable for a variety of applications. However, composite honeycomb is also the most expensive of the core materials discussed, making it unsuitable for many construction applications.
In the application of sandwich panels, the core material of the panel is the main determinant of its suitability for the application, especially in terms of its thermal and acoustic insulation properties, strength and stability, fire resistance and moisture resistance. Whichever core material is chosen, it is important to carefully consider the intended application to maximize the efficiency of the sandwich panel.